Part 1: Why Do We Cure Concrete?
To understand what is meant by curing concrete, let’s first refer to American Concrete Institute Report 116R, Cement and Concrete Terminology. This dictionary of industry terms defines curing as: “The action taken to maintain moisture and temperature conditions in a freshly placed cementitious mixture to allow hydraulic cement hydration and (if applicable) pozzolanic reactions to occur so that the potential properties of the mixture may develop.” In simpler terms, curing is what we do to fresh concrete to make sure it doesn’t dry out too quickly. The three primary benefits of properly curing new concrete are:
- Predictable strength gain: Laboratory tests show that concrete in a dry environment can lose as much as 50% of its potential strength compared to similar concrete that is moist cured. Concrete placed under high temperature conditions will gain early strength quickly but later strengths may be reduced. Concrete placed in cold weather will take longer to gain strength, delaying form removal and subsequent construction.
- Improved durability: Well-cured concrete has increased surface hardness and is more able to withstand surface wear and abrasion. Curing also makes concrete more watertight, thereby increasing freeze-thaw durability and service life.
- Better serviceability and appearance: A concrete slab that has been allowed to dry out too quickly is likely to have a soft surface with poor resistance to wear and abrasion. Proper curing reduces dusting and scaling.
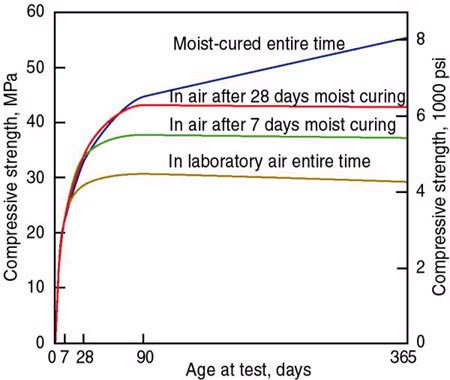
So what’s going inside the concrete when it is curing? First of all, the cementitious materials in concrete need water in order to chemically react and form a hard, durable matrix, or the “glue” that holds concrete together. This reaction between cementitious materials and water is called hydration, and it can continue for an extended period of time after concrete placement. A long, slow hydration process will result in concrete with optimal strength and durability. If fresh concrete is not properly cured and the mix water evaporates too quickly, there is likely to be unhydrated cementitious materials in the concrete. This can lead to the durability and strength problems mentioned earlier.
More specifically, improper curing can cause plastic shrinkage cracking, which occurs when moisture rapidly evaporates from a fresh concrete surface faster than the bleed water can appear to replace it. Stress in the new concrete surface resulting from this rapid drying causes the short, irregular cracks known as plastic shrinkage cracking. The use of an evaporation retardant while finishing, especially in dry or windy conditions, as well as implementing a proper curing method immediately after finishing can help prevent plastic shrinkage cracking.
Plastic shrinkage cracking, which usually occurs within the first twenty-four hours after placement, should not be confused with drying shrinkage, a longer-term condition that can occur when hardened concrete loses moisture. Drying shrinkage can actually continue for years after placement. Drying shrinkage is an inherent characteristic of hydraulic cement concrete; simply put, when concrete is wet, it expands. When it dries, it contracts or shrinks. This contraction is always subject to some form of restraint such as a structure’s foundation, or the reinforcing steel embedded in the concrete. The combination of shrinkage and restraint develops tensile stresses within the concrete – which, due to the inherently low tensile strength of concrete, will likely lead to cracking.
Temperature is another critical factor in proper curing, since the rate of hydration, and therefore, strength development, is faster at higher temperatures. Generally, concrete temperature should be maintained above 50°F (10°C) for an adequate rate of strength development. Further, a uniform temperature should be maintained through the concrete section while it is gaining strength to avoid thermal cracking. For exterior concrete, the ambient relative humidity and wind conditions are also important to monitor; they contribute to the rate of moisture loss from the concrete and could result in cracking, poor surface quality and durability.
Court Avenue in Bellefontaine, Ohio is an interesting case study on the importance of properly curing new concrete. Constructed in 1893, Court Avenue is known for being the first street in the United States to be paved with concrete. It was composed of two levels of concrete and included aggregate of no larger than ½ and 1½ inches (top and bottom layers respectively), with water-cement ratios of 0.45 and 0.60 (top and bottom), laid on a 4 inch (100 mm) deep base. Mixed by hand, the concrete has an air content of about 8% and a compressive strength slightly over 5,000 psi (34 MPa). Court Avenue, although now closed to vehicular traffic, is still in place and in great shape today.
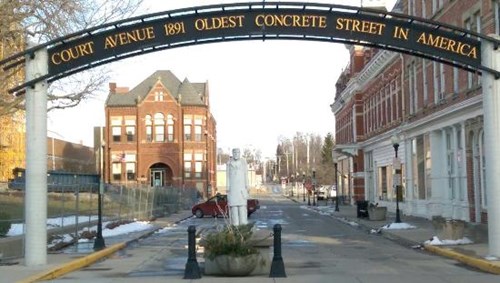
Why is this concrete, produced with simple materials, no reinforcement or admixtures, so durable? Our guess is because Court Avenue was cured by placing a 2 inch (50 mm) layer of wet sand on its surface and keeping it in place for 2 weeks.
Stay tuned for Part Two of the Demystifying Curing & Sealing series: How Do We Cure Concrete?
Jennifer Crisman is the Director of Marketing Services at Euclid Chemical. She can be reached at jcrisman@euclidchemical.com.